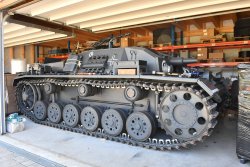
Our last visit to HERA Arms in Triefenstein was not so long ago. HERA boss Thomas Nöth had invited us to take a look at a replica of a Sturmgeschütz III assault gun. This time, however, it was not about this impressive collector's item, but Thomas Nöth promised us a look behind the scenes and into firearms manufacturing.
We were very much looking forward to this, because unlike many other manufacturers, HERA Arms consistently relies on production and development in-house and with two long-term partner companies in the region. This promises not only "Made in Germany" quality, but also direct influence of the owners of HERA Arms on the manufacturing quality and the corresponding quality guarantee at any time.
The manufacturing at HERA Arms in Germany
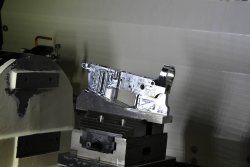
During our visit to the HERA factory, Thomas Nöth first took us through the mechanical production. This is where the metallic components and essential gun parts for your HERA firearms are manufactured. Lowers, uppers and other receiver parts are produced here on state-of-the-art machines from DMG Mori.
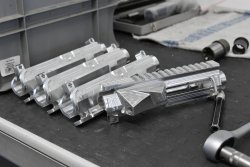
The machines are an important factor, explains Thomas Nöth, because only simultaneous milling with four or more axes can work very finely structured surfaces into the material. He shows us the result of this on a lower for the 9 mm AR The9er. Another example, the HERA 7SIX2 upper: its top rail, as well as the core drilling, are done in one operation to avoid even the smallest alignment mistakes.
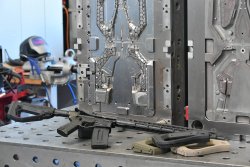
Not only the metal parts at HERA Arms are from HERA's own production. but also the polymer products. At the moment 30 molds are in use in the injection molding production line to manufacture attachments and accessories for the in-house products, but also for the AR-10/AR-15 system in general. It is quite impressive how big and heavy the machines are to cast partly very small components. During our visit, the new H7 stock for the Remington 700 system is being produced, which is also available as a complete gun at HERA Arms.
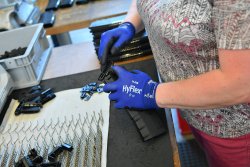
In this highly technical production with machines across the entire tonnage spectrum, man still plays an important role. Not only during the final production and assembly of the firearms, but also during the injection molding process.
The machine cycle for casting a magazine, for example, takes between 50 and 52 seconds. Meanwhile, the machine operators assemble the finished magazines from the magazine half-shells that have just been produced. This time, by the way, the new H3L magazine – a 10-round magazine the length of the 30-round variant. Originally developed for California, the magazine now also serves an important purpose for sports shooters. The H3L in fact combines the good manageability of a long magazine with the maximum capacity of 10 rounds.
If you have not already done so, we recommend that you watch our video and experience the impressions "live and in color".
We would like to thank Thomas Nöth of HERA Arms for this exciting factory tour and look forward to the upcoming test firearms from HERA!
Further information about the products from Triefenstein can be found on the new HERA Arms website.
Many new products for sports shooters and hunters from HERA Arms are presented here.